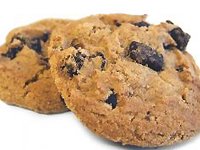
At first glance the baker’s trade doesn’t have much to do with manufacturing microchips. Yet a closer look at the utilization of the prime production area – here the baking tray, there the wafer – reveals quite a few areas of common ground. The semiconductor industry definitely has the edge though.
Analysis of the baking process shows a high percentage of fixed production costs. These are accounted for firstly, of course, by the bakehouse premises (we would say fab) and secondly by the mixing and kneading machines and ovens (we say equipment). The variable costs for eggs, flour and grain (in our case wafers, gases, electricity, water) are negligible. So the machinery is in place, it just needs to be used as efficiently as possible. Optimization of the saleable products per baking tray is the name of the game.
The crux of the matter is to increase the number of cookies per oven charge. To achieve this, a first step would see simply placing the cookies closer to one another, concealing virtually the entire baking tray. We try to do that, too. The individual chips are so close together as to allow only the diamond saw-blade or laser beam to pass through. This scoring line between the chips – the so called kerf – is today only about 50 micrometers wide (about the thickness of a human hair).
A second step would see increasing the number of cookies by downsizing them – at the same selling price, of course. This recommendation would work as long as the customer still recognizes the cookies as such and accepts them. Increasing the number of chips at the expense of size is common practice. It’s called “shrinking” the chips. And here semiconductor technology has a peerless advantage over all other worldly goods: the smaller chip functions just as well as its larger precursor. When it comes to the enclosed end product you can’t even tell the difference between the two versions and so they can command the same price. (At least in theory. If the customer is aware that the chip is smaller and was therefore manufactured more economically, he’ll try to beat down the price). This pattern of chip evolution, that the smaller and cheaper (i.e. the chip proper and ultimately the transistors) fill the bill just as well as - and often better than - the larger and more expensive, was once dubbed “God’s gift to man” by the scientist Yuan Taur. No other technology has undergone shrinkage on anything like this scale, and by no means over a period spanning more than four decades. Were the cookies to have been systematically downsized over this length of time, their nutritional value would meanwhile be infinitesimal.
Once the exercise of downsizing the cookies has reached the crunch point, the third stage of optimization would be introduced: larger trays and perforce larger ovens. The step to a larger wafer is witnessed about every five to seven years. A larger wafer accommodates a higher number of chips. This is so firstly because it is simply larger. Secondly, the chips can fill the peripheral area better due to the reduced curvature. The changeover to larger wafers calls for new machinery all down the line, entailing significant investment.
The final tip: twenty-four-seven baking for better utilization of the machinery and ovens. This is a step the baker reluctantly accepts. Needless to say though, production in the chip industry operates in shifts, day and night. Economic reasons dictate that the multibillion-dollar machinery must not be left idle at any time.Getting to grips with the immense fixed costs hence requires vast quantities. It is imperative to use the most precious commodity, the wafer surface, as efficiently as possible. Therefore it is not without good reason that it’s occasionally also referred to as ‘real estate’.At ground-root level many of our colleagues are doing nothing other than the baker next door: baking smaller and smaller cookies to increase the output per tray. It just remains to be hoped that they’ll also sell like hot cakes!
(copy-paste from internal IFX emag: Joe corner)
No comments:
Post a Comment